Two giant steps for EVs
Could these big breakthroughs in battery and charging technology shift the landscape for electric vehicles?
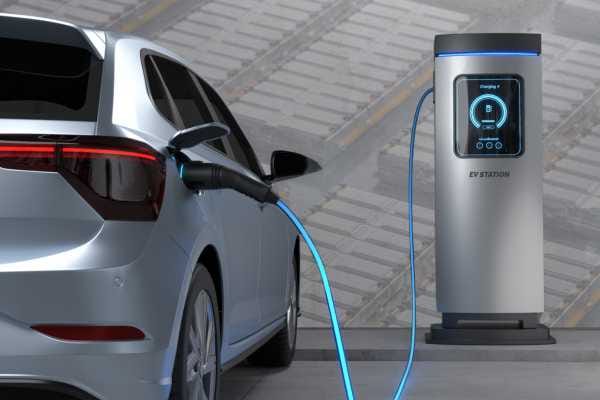
A new super-fast charging platform and a circular battery recycling facility offer a glimpse into our sustainable future.
The fast charging technology, dubbed the Super e-Platform, was unveiled last week by electric vehicle manufacturer BYD as the Chinese automaker continues to push boundaries in EV technology.
BYD’s system promises to slash charging times to as little as five minutes and ease range anxiety for drivers by delivering up to 1,000 kW of charging power.
In practical terms, that means an EV could gain around 400 kilometres of range in just five minutes – comparable with filling up a traditional fuel tank. In comparison, fast-charging infrastructure in Australia currently tops out at 350kW.
According to BYD, the first vehicles to feature its next-gen tech will be the Han L sedan and Tang L SUV, which are available for preorder in China.
To support this leap in technology, BYD says it plans to roll out over 4,000 ultra-fast charging stations across China. Details of the timeline for this, or an international expansion have not yet been announced.
Car batteries go circular
Marking a major step towards sustainable EV production, Europe’s first battery recycling plant began operations late last year in Southern Germany.
To build the facility, Mercedes-Benz partnered with Primobius, a joint venture between German engineering company SMS group and Australia's Neometals, which develops sustainable process technologies to recycle and recover critical materials from high-value waste streams.
Mercedes-Benz said its Kuppenheim facility worked on an integrated process called mechanical-hydrometallurgy with an aim to recover over 96 per cent of valuable materials such as lithium, nickel, and cobalt, to be reused in new battery cells.
According to Mercedes-Benz the plant will generate enough recycled material to produce more than 50,000 new battery modules annually, reducing reliance on supply of natural resources.
"The innovative technology enables us to recover valuable raw materials from the battery with the highest possible degree of purity."
With battery demand surging, the move signals a shift towards a circular economy in the EV industry, cutting waste and reducing emissions.
“The innovative technology enables us to recover valuable raw materials from the battery with the highest possible degree of purity,” said Mercedes-Benz production and supply chain manager, Jörg Burzer.
“This turns today's batteries into tomorrow's sustainable mine for raw materials.”
Unlike traditional pyrometallurgy, the company says its combined mechanical and hydrometallurgical process is less-intensive in terms of energy consumption and material waste because it operates at lower temperatures.
The Kuppenheim site also runs entirely on green electricity from a large roof-based photovoltaic system with peak output of more than 350 kilowatts.
Super e-Platform
The BYD platform will use a 1,000-volt architecture that is expected to enable peak charging speeds of up to 1,000 kilowatts, allowing about 400 kilometres of range in just five minutes. The first vehicles will be the Han L sedan and Tang L SUV, with a planned rollout in China of ultrafast charging stations.
Battery recycling
The Mercedes-Benz battery recycling plant first uses a mechanical process that sorts and separates plastics, copper, aluminium and iron under low process temperatures (up to 80C) that means it consumes less energy. The downstream hydrometallurgical process then targets so-called black mass that makes up the electrodes of the battery cells using a chemical process.