This world-first top is made from digested nylon
Reusing the nylon in old clothes to make new clothes has been impossible until now.
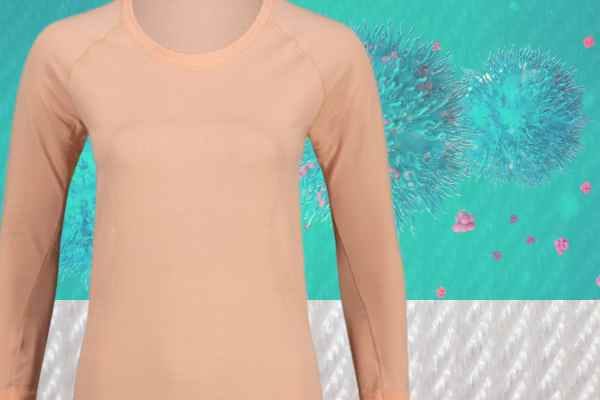
The infinite recycling of textiles is the fashion industry’s holy grail - and it’s one step closer thanks to enzymes.
This unassuming long-sleeved top is the first garment in the world to be made with enzymatically recycled nylon 6,6 – one of the most common types of nylon used in the fashion industry.
The garment – the Swiftly Tech long-sleeve top – has been unveiled by Canadian activewear brand Lululemon in partnership with Australian cleantech startup Samsara Eco.
Almost two-thirds of new clothes are made from polyester, acrylic, spandex and nylon fibres with their production accounting for millions of barrels of oil each year. Meanwhile, mountains of textile waste are sent to landfill, with less than one per cent of clothing recycled into new textile fibres.
Recycled nylon has previously been produced from post-industrial material waste, but Samsara Eco has pioneered a patent-pending enzymatic recycling process to create the world’s first fibre-to-fibre recycled nylon 6,6 garment.
Its technology uses engineered enzymes to break down nylon 6,6 synthetic blends, enabling them to be turned back into new clothes which, once scaled up, opens up new sustainability options for the apparel industry.
The Swiftly, which is currently available in the form of samples, uses over 90 per cent of nylon textile waste that’s been enzymatically recycled and according to Lululemon has the same fit, feel and quality as existing products.
"This is an incredibly significant moment for the future of sustainable fashion and circularity."
“The Lululemon Swiftly top samples go beyond material innovation – they represent the exciting possibilities and impact that can be achieved through collaboration and cross-industry partnership,” Lululemon’s Vice President of Raw Materials Innovation Yogendra Dandapure says.
“This breakthrough not only signals a turning point for sustainable innovation in apparel, but for all industries looking to shift towards more circular models."
CEO and Founder of Samsara Eco Paul Riley says, “Our work with Lululemon represents a ground-breaking step forward in tackling the challenge of textile waste and demonstrates the potential to create a fully circular ecosystem for apparel.
“We’ve started with nylon 6,6, but this sets the trajectory of what’s possible for recycling across a range of industries as we continue expanding our library of plastic-eating enzymes.
"This is an incredibly significant moment for the future of sustainable fashion and circularity.”
Eco fashion obstacles
Innovation in emerging sustainable textiles remains strong, but scaling up is proving perilous for some startups in the space.
Cotton textile recycling pioneer Renewcell recently filed for bankruptcy after failing to raise sufficient funding, despite attracting some heavy-hitting partners including H&M. The Swedish startup cited slow industry takeup of innovative fibres, but hopes to continue as a going concern under new ownership. Last year Bolt Threads halted production of its mycelium leather product Mylo under similar circumstances.
Lululemon, which uses nylon 6,6 as a foundational fibre for many of its bestselling garments, announced plans to collaborate on enzymatically recycled nylon with Samsara Eco last year.
"We look forward to continuing to work with Samsara Eco to help scale this new technology in the months and years ahead,” Dandapure says.
Samsara Eco, meanwhile, has raised A$54 million in a series A funding round led by venture capital firm Main Sequence in order to propel its commercialisation ambitions with the creation of a new research and development facility which is due to open near Canberra, Australia this year.
Samsara Eco has developed an enzymatic technology that recycles plastics in collaboration with the Australian National University. The patent-pending depolymerisation process converts plastics back to their original monomers for reuse as recycled inputs in the production of new plastics in an energy and cost effective way, allowing for infinite recycling.