Why these small balls are big news
Could these unassuming stainless-steel balls hold the key to the widespread adoption of clean energy?
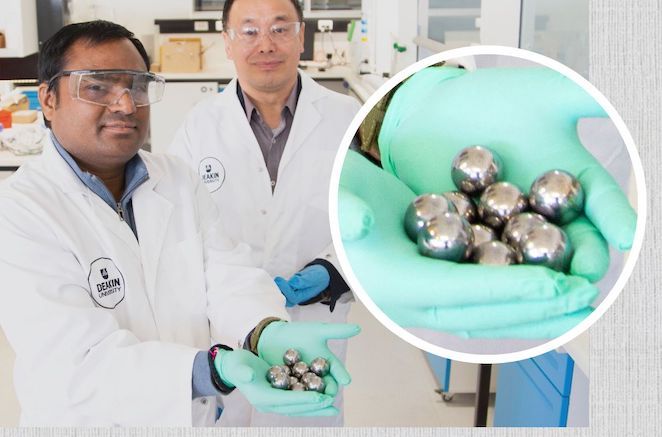
Could these unassuming stainless-steel balls hold the key to the widespread adoption of clean, green hydrogen gas?
Although green hydrogen gas holds great promise as a renewable fuel source, safe storage and transportation are considered major hurdles to its uptake.
However, a brand new process discovered by nanotechnology researchers from Deakin University may provide a new way to safely separate, store and transport huge amounts of the gas.
By adopting a completely different mechanochemical way of separating and storing gases the researchers believe they can improve its safety with a process that uses just a fraction of the energy.
They say the key ingredient used in their process is boron nitride powder, which is able to absorb substances because it is small but has a large amount of surface area.
Once absorbed into this material, the gas can be transported safely and easily. Then, when the gas is needed, the powder can be simply heated in a vacuum to release the gas unchanged.
The boron nitride powder can be reused many times to carry out the same gas separation and storage process again and again, according to lead researcher Dr Srikanth Mateti.
“There is no waste, the process requires no harsh chemicals and creates no by-products. Boron nitride itself is classified as a level-0 chemical, something that is deemed perfectly safe to have in your house.
“This means you could store hydrogen anywhere and use it whenever it’s needed,” Dr Mateti said.
"We were so surprised to see this happen, but each time we kept getting the exact same result, it was a eureka moment."
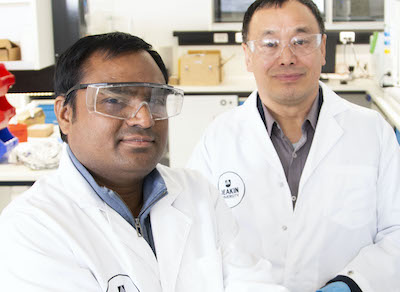
The breakthrough is the culmination of three decades of work by a team led by the University’s Chair of Nanotechnology, Professor Ying (Ian) Chen.
“The current way of storing hydrogen is in a high-pressure tank, or by cooling the gas down to a liquid form. Both require large amounts of energy, as well as dangerous processes and chemicals,” Professor Chen said.
“We show there’s a mechanochemical alternative, using ball milling to store gas in the nanomaterial at room temperature. It doesn’t require high pressure or low temperatures, so it would offer a much cheaper and safer way to develop things like hydrogen powered vehicles.”
The new process could help create solid state storage technologies for a range of gases, and the same breakthrough also has the potential to make oil refineries greener by drastically cutting the emissions created by separating crude oil into the different gases used by consumers, such as petrol or household gas.
The current separation process is based on high-energy ‘cryogenic distillation’ and uses a whopping 15 per cent of the world’s energy.
The ball-milling gas absorption process, in contrast, consumes 76.8 KJ/s to store and separate 1000L of gases, at least 90 per cent less than the energy used in the petroleum industry’s current separation process, according to the researchers.
Lead researcher Dr Srikanth Mateti said that the breakthrough is so significant, and such a departure from accepted wisdom on gas separation and storage, that he had to repeat his experiment 20 to 30 times before he could believe it.
“We were so surprised to see this happen, but each time we kept getting the exact same result, it was a eureka moment,” Dr Mateti said.
So far the team has been able to test their process on a small scale, separating about two to three litres of material. They hope with industry support that can be scaled up to a full pilot and they have submitted a provisional patent application for their process.
“We need to further validate this method with industry to develop a practical application,” Professor Chen said.
“To move this from the laboratory to a larger industry scale we need to verify that this process is cost saving, more efficient, and quicker than traditional methods of gas separation and storage.”
The tech
Nanotechnology researchers from Deakin University in Australia have described a new way to safely separate, store and transport huge amounts of gas in the journal, Materials Today. The new process could help create solid state storage technologies for a range of gases, including the safe storage and transportation of hydrogen – a major barrier to widespread take-up of the sustainable gas. The key ingredient used in the new mechanochemical process is boron nitride powder, which is placed into a ball mill along with the gases that need to be separated. During the process, the boron nitride powder is placed into a ball mill – a type of grinder containing small stainless-steel balls in a chamber – along with the gases that need to be separated. As the chamber rotates at a higher and higher speed, the collision of the balls with the powder and the wall of the chamber triggers a special mechanochemical reaction resulting in gas being absorbed into the powder.
Who funds it
The Deakin University researchers have submitted a provisional patent application for their process and they hope that with industry support it can be scaled up to a full pilot.
Is it ready to roll
So far the team has tested their process on a small scale, separating about two to three litres of material. They say they need to further validate this method with industry to develop a practical application.