Surfboards from old wind turbines
Tough-to-recycle wind turbine blades are finding favour with sport and fashion brands in search of hard-wearing sustainable materials.
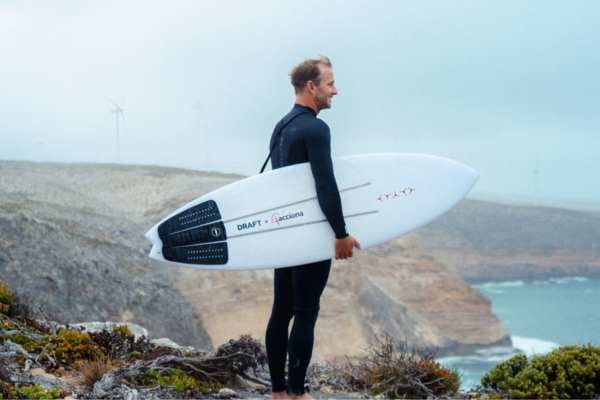
A retired wind turbine blade from Victoria’s Waubra wind farm has been transformed into a set of high-performance surfboards.
In a world-first for sustainable manufacturing, professional surfer Josh Kerr and his surfboard brand Draft Surf have created surfboards from repurposed wind turbines.
In partnership with renewable energy giant Acciona Energia, the first ten prototype boards were crafted on the Gold Coast and integrate repurposed turbine blade strips within the deck to enhance strength and flex control.
Recycled fibreglass was used to create the fins, while particulate from the turbine blade was incorporated into the fibreglass outer shell for added durability.
The project is part of Acciona’s 'Turbine Made' initiative, with expressions of interest for Australian innovators announced last month to seek new ways to transform decommissioned wind turbine blades.
“When Acciona approached us about being part of the solution and working together to create these surfboards, we jumped at the opportunity,” Kerr said. “At its core, our brand is about enabling the best surfing experience with quality products, in a sustainable way.”
"We know that in the next five to ten years, countries like Australia will have a large volume of decommissioned wind turbine blades, so we’re acting now to explore new ways to recycle and reuse the material they are built from."
With wind energy infrastructure expanding, the challenge of managing decommissioned turbine blades is a pressing issue, with some regions considering laws to prohibit their disposal in landfill.
Turbines typically last around 25 years, and there are 31 wind farms in Australia that are older than 15 years old, based on 2023 figures from the Clean Energy Council.
Caroline Pinter, brand and marketing manager for Acciona Energía said the blade material could be used to create a vast range of products "from children’s playgrounds and koala crossings for highways, to flame-resistant clothing for firefighters, homes for butterflies and artificial reefs".
Acciona's Energia's global sustainability director Mariola Domenech said the project highlighted the company’s commitment to circular economy principles.
“We know that in the next five to ten years, countries like Australia will have a large volume of decommissioned wind turbine blades, so we’re acting now to explore new ways to recycle and reuse the material they are built from,” Domenech said.
“The creation of a surfboard prototype, developed locally, is an example of how we're reimagining the materials from decommissioned turbine blades and pushing the envelope of innovation when it comes to the circular economy.”
Footsteps for the future
In a similar recent initiative, Acciona Energia joined forces with Spanish footwear brand El Ganso to create sustainable sneakers that included recycled blade material from a local wind farm in their soles.
Late last year energy company Vattenfall showcased a repurposed wind turbine nacelle shell from an Austrian wind farm that had been transformed into a tiny home as part of a design initiative to rethink the future footprint of decommissioned turbines.
Taking a different approach to the issue is wind turbine manufacturer Siemens Gamesa which in 2021 announced it had developed a ‘RecyclableBlade’ based on a new type of resin that simplify the material separation process for recycling turbine blades.
Wind turbines are predominantly made of composite materials, which are challenging to recycle. To create the line of surfboards Acciona repurposed a decommissioned blade from the Waubra Wind Farm in Victoria by breaking it down into a versatile particulate that could serve as a raw material. The surfboards incorporate strips of these repurposed wind turbine blades into the deck to enhance performance, while the fins are crafted from recycled fibreglass. The fibreglassing process also integrates particulate from the blade material, further strengthening the outer shell.