‘Out of the box’ carbon capture
Smaller emitters may soon tap into shipping container-sized modular carbon capture solutions.
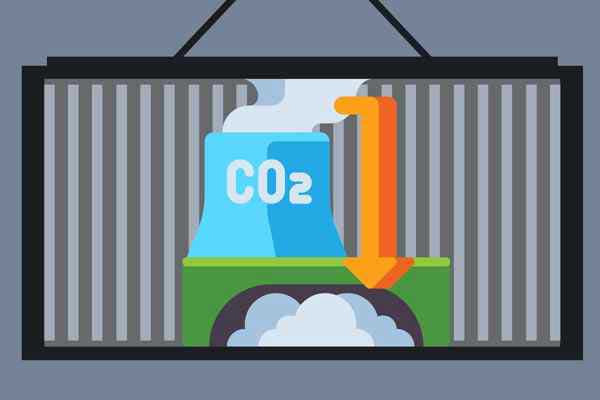
Smaller emitters may soon tap into shipping container-sized modular solutions.
While it cops flak for prolonging dependence on fossil fuels, carbon capture technology is also acknowledged as an important short-term step in decarbonising some industries.
Until recently, carbon capture solutions have largely been limited to large, custom-built projects running into hundreds of millions of dollars.
Now, smaller mass-produced units are headed to market as a number of companies develop modular solutions for smaller emitters such as biogas plants, municipal waste incinerators, cement plants and ships.
Japan’s Mitsubishi Heavy Industries (MHI) is among those developing small to medium-sized carbon capture systems and its range will be launched next year.
These smaller, standardised solutions capture flue gas and convert this into liquid or gaseous CO2 which can then be used in agriculture, forestry, and the food and beverage industry.
Other companies also marketing out-of-the-box, modular solutions include UK company Carbon Clean, and Dutch company Bright Renewables.
MHI says that over the past year more than 100 companies have expressed interest in its modular capture system, which will be available from next year. The system can capture between 0.3 to 200 metric tons of CO₂ a day and uses an amine-based solution.
"By fully consuming all captured CO2 at its carbon-negative power plant, Taihei Dengyo looks to help prevent global warming and promote a decarbonised society."
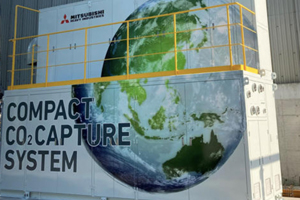
Small and medium-sized carbon capture units can sequester up to 95% of CO₂ emissions, will come ready-made, be mass-produced and can be easily transported and installed, says MHI.
One of MHI’s new systems recently went into commercial operation at a biomass power plant in Hiroshima.
The power plant burns wood chips and is operated by Taihei Dengyo Kaisha in the suburb of Seifu Shinto in Hiroshima City. CO2 captured from the plant’s flue gas will be used for growing tomatoes and strawberries in on-site greenhouses.
“By fully consuming all captured CO2 at its carbon-negative power plant, Taihei Dengyo looks to help prevent global warming and promote a decarbonised society,” MHI says.
The system has the capacity to capture 0.3 metric tons of carbon per day – and it currently captures about 0.3% of the plant’s total emissions.
It measures five meters in length and two meters wide, and the modular configuration enabled rapid transportation to the site and easy installation, according to MHI.
Going forward, the MHI system line-up will be expanded to capture carbon from diverse emission sources worldwide and include operational support services using a remote monitoring system.
The tech
A biomass power plant has installed a compact carbon capture system in Seifu Shinto, a suburb of Hiroshima City. The system has the capacity to capture 0.3 metric tons per day and is based on a standardised design created by Mitsubishi Heavy Industries (MHI). The system is five meters in length and two meters wide and can be transported from the factory by truck. The CO2 capture technology used is the KM CDR Process, jointly developed by MHI and Kansai Electric Power, which applies a high-performance KS-1 amine solvent – a technology that MHI says significantly reduces energy consumption. Carbon Clean and Bright Renewables modular systems also use amine technology.
Who funds it
The CO2 capture technology used by Mitsubishi Heavy Industries is the KM CDR Process which uses a high-performance KS-1 amine solvent which the Japanese company jointly developed with Kansai Electric Power.
Is it ready to roll
The MHI system will roll out commercially in 2023 and the line-up will be expanded to capture carbon from diverse emission sources and will include operational support services using a remote monitoring system.