Closing the loop on Nylon
Nylon recycling is a step closer with this first-of-its-kind 'enzymatic' facility.
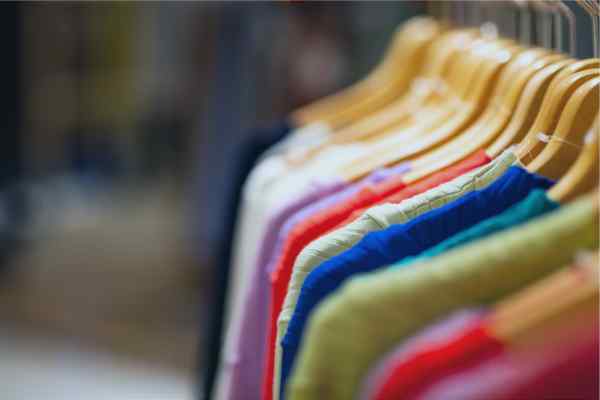
Nylon 6,6 is widely used in performance apparel and fashion, but recycling it has been notoriously difficult. A world-first recycling facility could soon change that.
Australian recycling tech startup Samsara Eco and leading nylon 6,6 manufacturer Nilit have signed a Memorandum of Understanding (MOU) to explore the construction of a pilot recycling facility for nylon 6,6.
The proposed facility, which would be located in Southeast Asia, aims to establish a new enzymatic textile-to-textile recycling process for nylon 6,6.
The infinite recycling of textiles is considered the holy grail of the fashion industry. The new facility is a step towards achieving this, enabling brands to create brand-new fabrics from recycled materials.
Globally, around four million tonnes of nylon 6,6 are produced annually and most ends up in landfill or is incinerated. The creation of this facility could revolutionise its end-of-life handling.
"Our vision is to deliver climate repair through infinite recycling. One of the ways we’re achieving this is by creating the first circular pathway for nylon 6,6."
Samsara Eco has developed a patented carbon-neutral enzymatic recycling process that enables fibre-to-fibre recycling of nylon 6,6. This technology was first used in March to create the Swiftly Tech long-sleeve top, the world's first garment made with enzymatically recycled nylon 6,6, by Canadian activewear brand Lululemon.
In June, Samsara Eco raised $100 million from a group of new and existing investors, including Singapore’s Temasek, Australian funds Main Sequence and Titanium Ventures, leisurewear giant Lululemon, Wollemi Capital, Japan’s Hitachi Ventures, and US venture capital group DCVC.
The funding, Samsara Eco said at the time, would help it scale its enzymatic recycling capabilities.
A good yarn
The planned facility will focus on recycling textile waste to produce sustainable nylon yarns and fabrics under Nilit’s Sensil brand. It is expected to be operational by late 2026 and will turn textile waste into high-quality recycled nylon 6,6 polymers that textile manufacturers can reuse indefinitely.
“Discarded clothing made from nylon 6,6, such as activewear, and even products like car interiors, typically end up in landfills or are incinerated at the end of life, which has dire consequences for our planet,” Samsara Eco CEO and founder Paul Riley said.
“Our vision is to deliver climate repair through infinite recycling. One of the ways we’re achieving this is by creating the first circular pathway for nylon 6,6.”
Nilit general manager Ilan Melamed said, “Nilit’s partnership with Samsara Eco is a critical step in our multi-pronged strategy to provide the apparel market with premium nylon 6,6 products that have a lower environmental impact.
“Implementing textile-to-textile recycling solutions will substantially decrease global carbon emissions and reduce the 92 million tonnes of textile waste added to landfills annually.”
Samsara Eco, in collaboration with the Australian National University, has developed an enzymatic technology that recycles plastics. This patent-pending depolymerisation process converts plastics back into their original building blocks, known as monomers, which can then be reused in the production of new plastics. This method is both energy- and cost-efficient, allowing for infinite recycling.