A concrete solution to slash emissions
It is the cornerstone of building projects the world over – and is also one of the biggest carbon emitters.
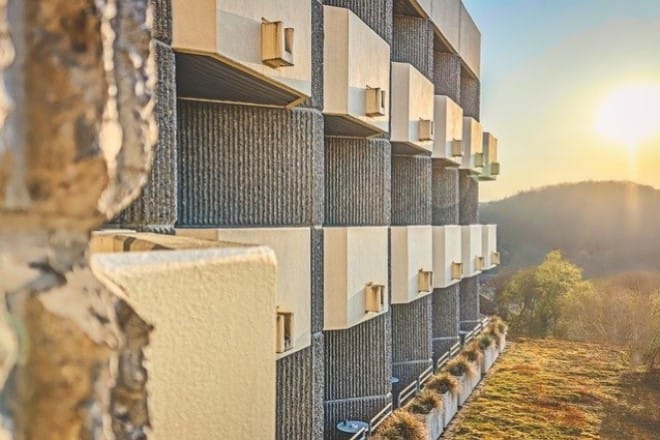
Cement – it’s not a big deal, right? Wrong.
It is the cornerstone of building and infrastructure projects the world over – and it’s also one of the biggest carbon emitters of all time.
Making concrete generates a whopping eight per cent of man-made carbon emissions, but Swiss scientists have come up with a solution that could slice these emissions by up to 40 per cent — and it’s called limestone calcined clay cement, or LC3 for short.
LC3 is a low carbon cement developed by Ecole Polytechnique Federale de Lausanne (EPFL) in Switzerland. By tweaking the recipe of cement to include calcined (heated) clay, it has the capability to dramatically slash emissions.
The catch is that just like normal cement, LC3’s makeup varies from location to location depending on the materials available there. This localisation process is already underway with trials and, in some cases, commercial production kicking off in places like India, Cuba, Columbia and Ivory Coast.
Heating limestone is the problematic part of the traditional concrete production process, say experts. While it’s not especially carbon intensive as manufacturing processes go, the sheer scale of the industry (cement is said to be the most used substance on earth after water) makes it the biggest emitter of all the things we manufacture. Moreover, global demand for cement is expected to double by 2050, driven by growing demand in emerging economies.
"The global impact of this technology cannot be underestimated. Here we have one single technology which can be implemented today which can really save at least one per cent of world CO2."
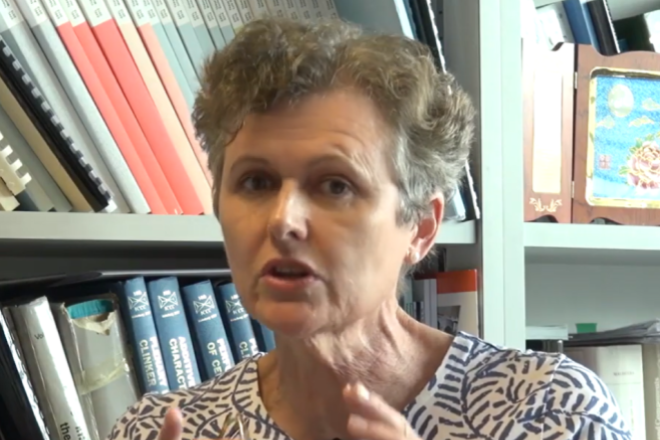
Manufacturing in all its forms contributes almost a third of global greenhouse gas emissions, and concrete, steel and plastic top the list, explains Bill Gates in his recently released book How to Avoid a Climate Disaster. He breaks it down like this: Making things (eg cement, steel, plastic) contributes 31 per cent of emissions, followed by plugging in (electricity) at 27 per cent, growing things (plants & animals) at 19 per cent, getting around (planes, trucks, cargo ships) at 16 per cent, and keeping warm and cool (heating, cooling and refrigeration) at 7 per cent.
Gates writes that while things like electricity get the most attention, cement is still one of the toughest problems to solve as no solutions currently exist to reduce emissions to zero.
LC3 is no exception, but even a 40 per cent reduction would make a massive and immediate impact on emissions, says cement research and director of EPFL’s Laboratory of Construction Materials, Karen Scrivener.
“The global impact of this technology cannot be underestimated. Here we have one single technology which can be implemented today which can really save at least one per cent of world CO2,” she says.
“And the timing is very important because in fact we are talking about a total amount of CO2 in the atmosphere to slow down climate change, so its much more important to act quickly to save CO2 today, than maybe have some wonder solution that can only be applied in fifty years.”
EPFL has been able to scale up LC3 development, testing and global collaboration thanks to funding from the Swiss Agency for Development and Cooperation through its Global Programme in Climate Change.
The tech:
C02 is given off in the manufacture of traditional cement when limestone and clay are heated to produce clinker, which acts as a binder in traditional cement products. Ecole Polytechnique Federale de Lausanne (EPFL) has found it can maintain the properties of traditional cement but reduce the CO2 emissions produced in its manufacture by up to 40 per cent by reducing the amount of clinker, replacing it with unheated limestone and calcined (heated) clays, which are both abundant materials that can found all over the world.
Who funds it:
The Ecole Polytechnique Federale de Lausanne (EPFL) has received 4m Swiss francs in funding from the Swiss Agency for Development and Cooperation to help it scale up LC3.
Is it ready to roll:
LC3 manufacture (and use) is in its early stages in India, Cuba, Columbia and Ivory Coast, with more large cement companies said to be looking to introduce it into their plants soon.